TURN KEY TRACEABILITY SOLUTION
An important Japanese automotive car manufacturer with the highest capacity vehicle output in the UK requested a high level of data traceability including accurate logging of torque values against VIN numbers.
The system has been installed across their production line during 2015 on all their existing DC tool systems. It is used to monitor and record torque results across the full final assembly line and gives full and accurate torque traceability for all vehicles. It guarantees robust quality gates to ensure only vehicles with acceptable torque fittings will leave the factory.
Ansomat supplied a complete turnkey package including the design, manufacture, supply, installation and commissioning of a set of facilities to monitor and track vehicles and sub-components, control and log data from all existing DC tool controllers and archive the data on the manufacturer sever.
The system is open and flexible and allows changes to be made in house with no specialist software skills.
It is designed to incorporate up to 600 DC tools across 120 stations, take a total of 12 check and repair stations on line and 5 stations off line and is flexible enough to upgrade this number according the customer’s needs.
The system includes a robust and very accurate vehicle and sub assembly tracking system. It interacts with the torque controllers to ensure the correct program is used on each vehicle and that data is stored against the correct vehicle or part. A plant broadcast has been supplied to the system which gives the order of vehicles in the line, plus information to configure the torque requirements per vehicle. The system interfaces with the customer systems to receive vehicle information and pass completed vehicle data to other customer systems.

The concept of the tracking system was to provide a vehicle tracking solution to ensure the exact position of each vehicle along the entire length of the production line. This has been achieved by two encoders mounted on the drives for each production line (5 lines in total). The two encoders works in tandem with each other in a master/slave relationship thus offering greater reliability combined with error checking/redundancy.
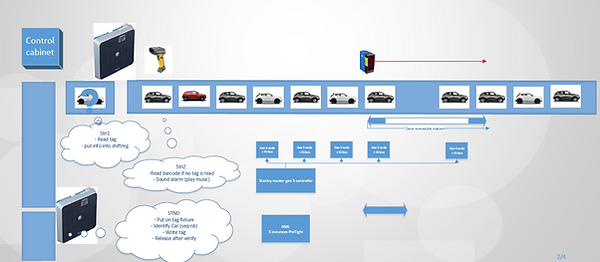
This methodology enables the control software to know the position along the track of every vehicle entering the production line enabling them to control and distribute the correct build information to all of the tightening stations along the line.
The expected vehicle entering the station and the current status of confirmation is clearly shown. There are configurable alarms and warnings to show the current status to the operator and request for actions. There is an option to access an overview of the line showing the vehicles in each station on any tracked conveyor (including sub conveyors). Vehicle information including model, colour and grade is available.
The HMI also show the gaps in the line and give the operator (with admin rights) the possibility to change the data in case of a vehicle removal. All vehicle ID scans are used by the system to compare against the expected vehicle/part and required alarms/warning/line stop logic implemented. If the vehicle tracking system is down, the line can still be in production by use of the override switch located at each controller bank.
Summarized, the following responsibilities have been implemented:
-
All current models with their allocated torque programs
-
All vehicle tracking requirements with adequate control to achieve 100% accuracy
-
Communication protocols to obtain tracking information from sub assembly conveyors
-
Kitting area systems with the required operator control/feedback and PLC I/O
-
Part verification stations on line with required operator feedback
-
Tooling to control the required I/O format
-
Tooling have been connected to the customer supplied network point and have been installed on a HMI on each controller bank
-
The torque profiles for individual tools/zones
-
Tool shuttle and lazy arm tracking system
-
Check and repair stations including HMI’s, operator warning systems and barcode
readers on off line systems
-
All shop floor PC/barcode hardware